auditorías de aire
Graco ofrece Auditorias de Aire para sistemas de Aire Comprimido, las cuales son diseñadas para proveer los mejores métodos para maximizar la eficiencia del sistema de aire comprimido. Dichas auditorias son económicas y al mismo tiempo efectivas.
Las auditorias de aire proporcionarán una solución para maximizar la energía requerida para producir aire comprimido mientras se entrega el aire al sistema a una baja presión.
¿qué es una auditoría de aire?
La auditoría de aire es una herramienta para maximizar la eficiencia del sistema de aire comprimido en planta, mediante la revisión completa de la generación de aire comprimido donde se presenta hasta el 85% de gasto energético no productivo, y el punto de uso que representa un 15% de pérdida de dinero por usos inapropiados del sistema.
Se utilizan data loggers para documentar el desempeño del sistema, se miden múltiples características simultáneamente durante varios días (presión, potencia, flujo, punto de rocío, etc.)
La Auditoría de Aire nos permite evaluar a detalle todas las áreas de oportunidad,crear un plan de acción para una solución viable de cada una de ellas y conocerlos costos reales de operación del Aire Comprimido.
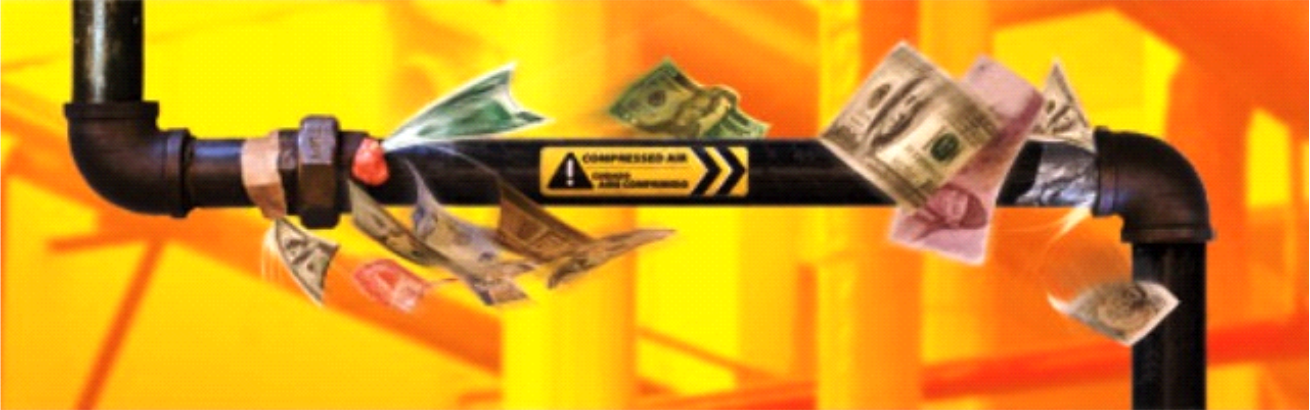
auditoría nivel 1 air insite
Incluyen los parámetros mínimos para una evaluación eficaz del sistema de aire comprimido, mediante la medición de Potencia, caídas de presión y el cálculo estimado del flujo por la eficiencia de los equipos. Por el lado de la generación se evalúan los compresores de aire comprimido y equipos de tratamiento. Por el lado de la demanda, se evalúa la tubería de distribución y puntos de uso. Estas auditorías proporcionan un plan operativo sólido y sirven como base para los programas de seguimiento y mejoras.

1.Mediciones
- a)Amperaje de Motores
- b)Caídas de Presión en el sistema
- c)Set Point de compresores
2.Cálculo de Flujo en base de la eficiencia de los equipos
3.Revisión visual del sistema
4.Reporte con Análisis, conclusiones y recomendaciones
auditoría nivel 2 air master
Evaluación totalmente medida y logramos visualizar una tendencia de los flujos de aire y presión en diversos sectores para su posterior análisis. Con estas revisiones del sistema se logra tener entre otras cosas:
Una visión general del sistema. Desarrollar planes a corto y largo plazo para establecer un control básico y gestión del sistema de aire. Una guía general que el usuario puede seguir para continuar aumentando la eficiencia del sistema. Identificación de programas específicos y / o acciones a desarrollar, además de los costos estimados y recuperación de la inversión.
1.Mediciones
- a) Flujo Total en SCFM
- b) Amperaje de Motores
- c) Presión de Descarga y del Sistema
- d) Caídas de Presión del Sistema
- e) Punto de Rocío
- f) Temperaturas de Aire
- g) Temperaturas de Sistema de Refrigeración
- h) Medición de partículas de aceite
2.Detección de fugas
3.Revisión visual del sistema completo
4.Elaboración de perfiles de Flujo y potencia por cada equipo
5.Simulador de consumo energético de 4 a 7 días
6.Revisión de usuarios Críticos de Presión y Flujo
7.Revisión de usos inapropiados de aire comprimido
8.Elaboración de reporte con análisis, gráficos, tablas, situación actual, configuración recomendada, conclusiones y propuestas de mejora a corto y largo plazo.
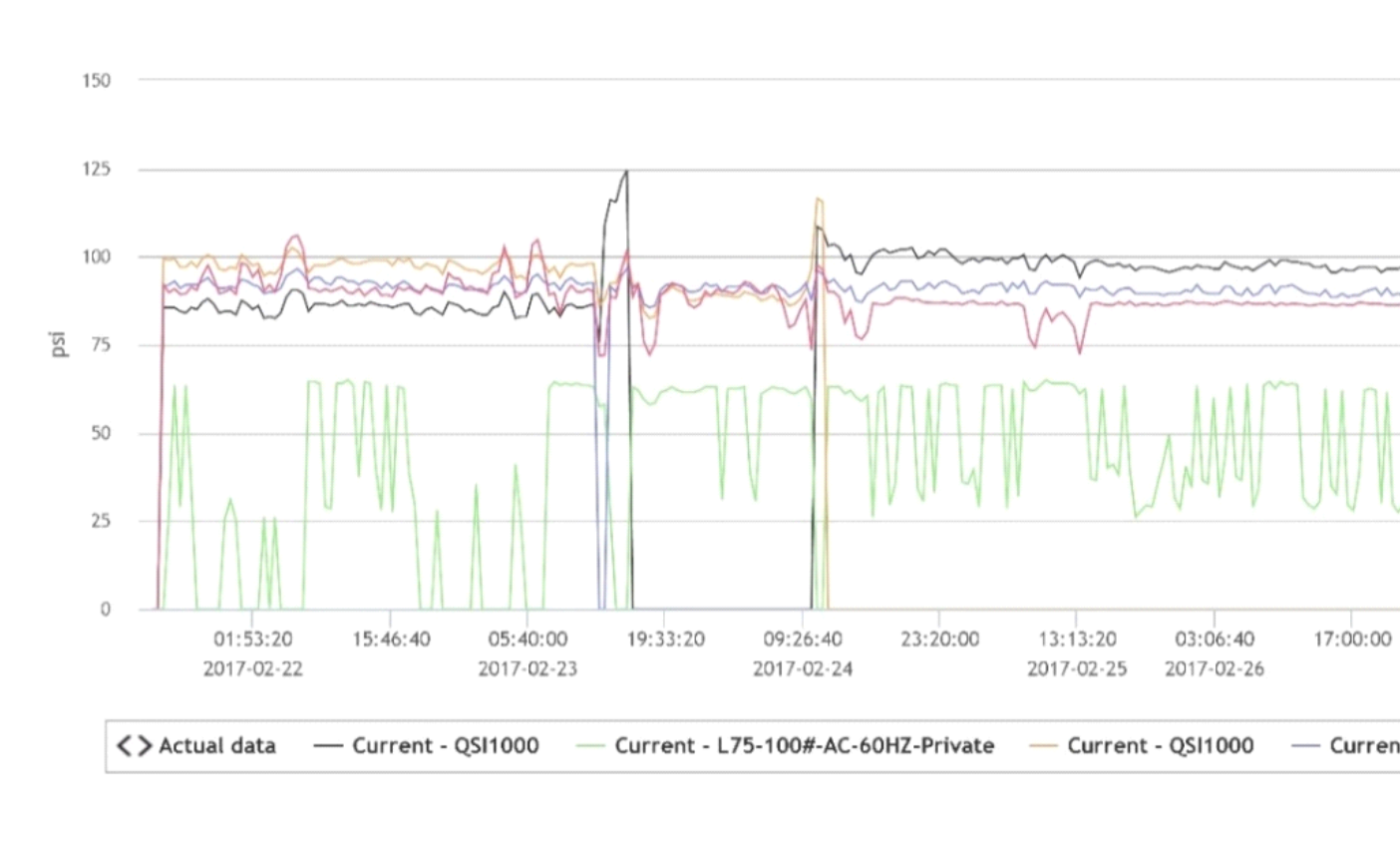
consecuencias de un sistema ineficiente
En la industria actual, es muy común observar sistemas de aire comprimido en malas condiciones debido a la falta de atención de parte de la empresa; el 100% de estos casos ocasionan problemas con la calidad del producto final del cliente, pueden ser rechazos de material o simplemente alto consumo en mantenimientos de maquinas o herramientas, además de paros de producción por los largos tiempos de entrega del refaccionamiento a sustituir.
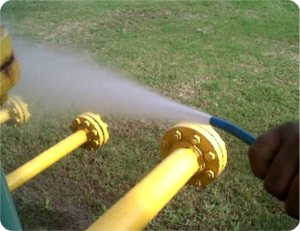
HUMEDAD EN LA RED NEUMÁTICA
El agua es uno de los problemas mas comunes en la industria y es ocasionada por la condensación del vapor de agua, a este punto de condensación se le conoce como Punto de rocío y se mide en °C o °F; este problema impacta principalmente en el daño de maquinaria y herramientas indispensables para la producción y en algunas aplicaciones también afecta en la calidad del producto.
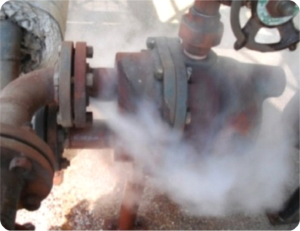
FUGAS
Este problema es ocasionado por los cambios de temperatura y la oxidación de las tuberías neumáticas, en su mayoría se dan en cada conexión roscada, con la expansión y contracción se forman pequeños orificios por los que se escapa una pequeña cantidad de aire, que sumadas todas representan un gasto de hasta el 30% del consumo energético del compresor
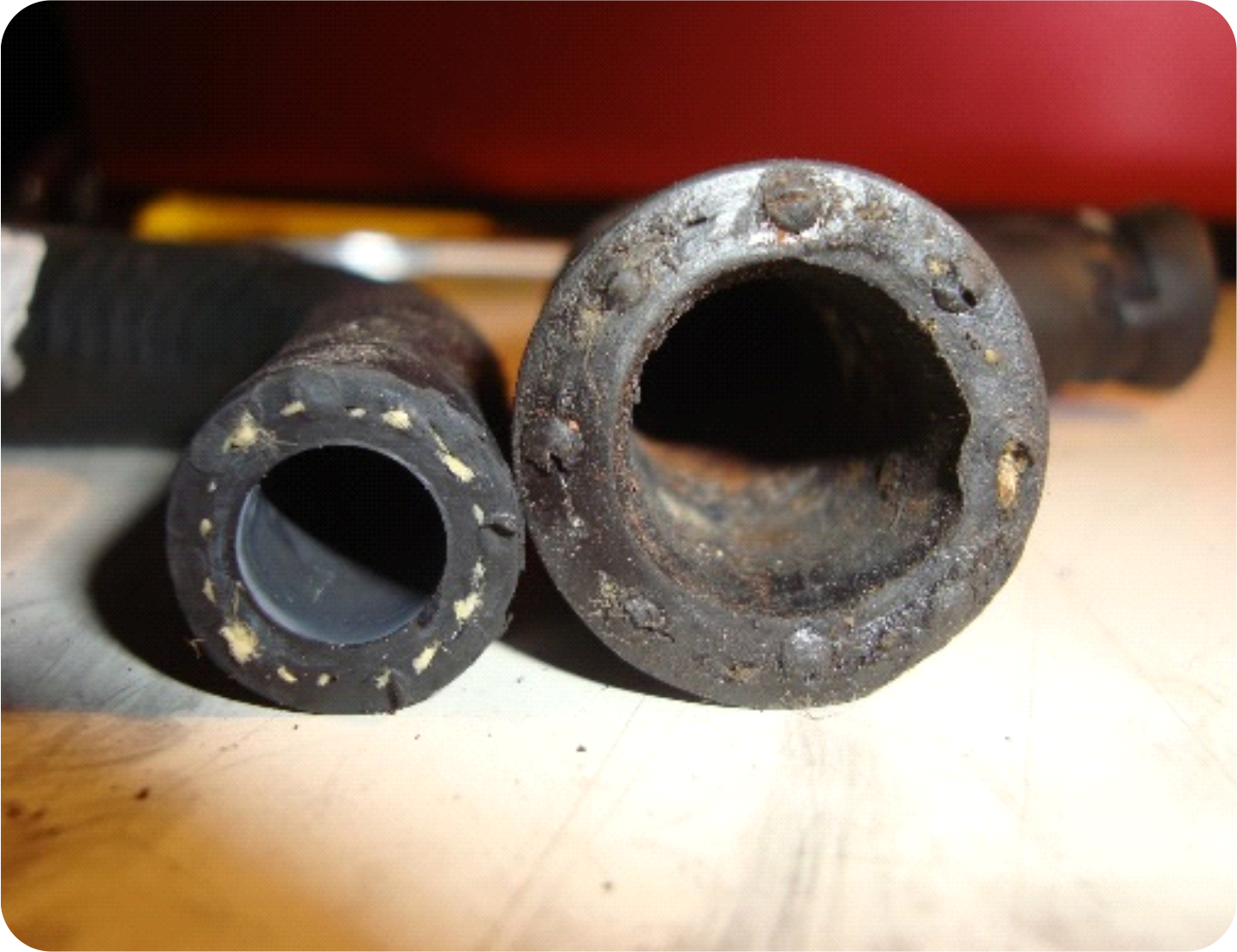
ACEITE Y PARTICULAS DE HIDROCARBUROS EN EL AIRE COMPRIMIDO
La principal causa de este problema radica en el desgaste de los compresores y la ineficiencia de los filtros que llevan para eliminar este residuo; otra de las causas es la contaminación ambiental que al llevar una gran cantidad de hidrocarburos mezclados en el aire y al realizar la compresión se unen formando pequeñas gotas y dañando los componentes neumáticos y el producto del cliente.
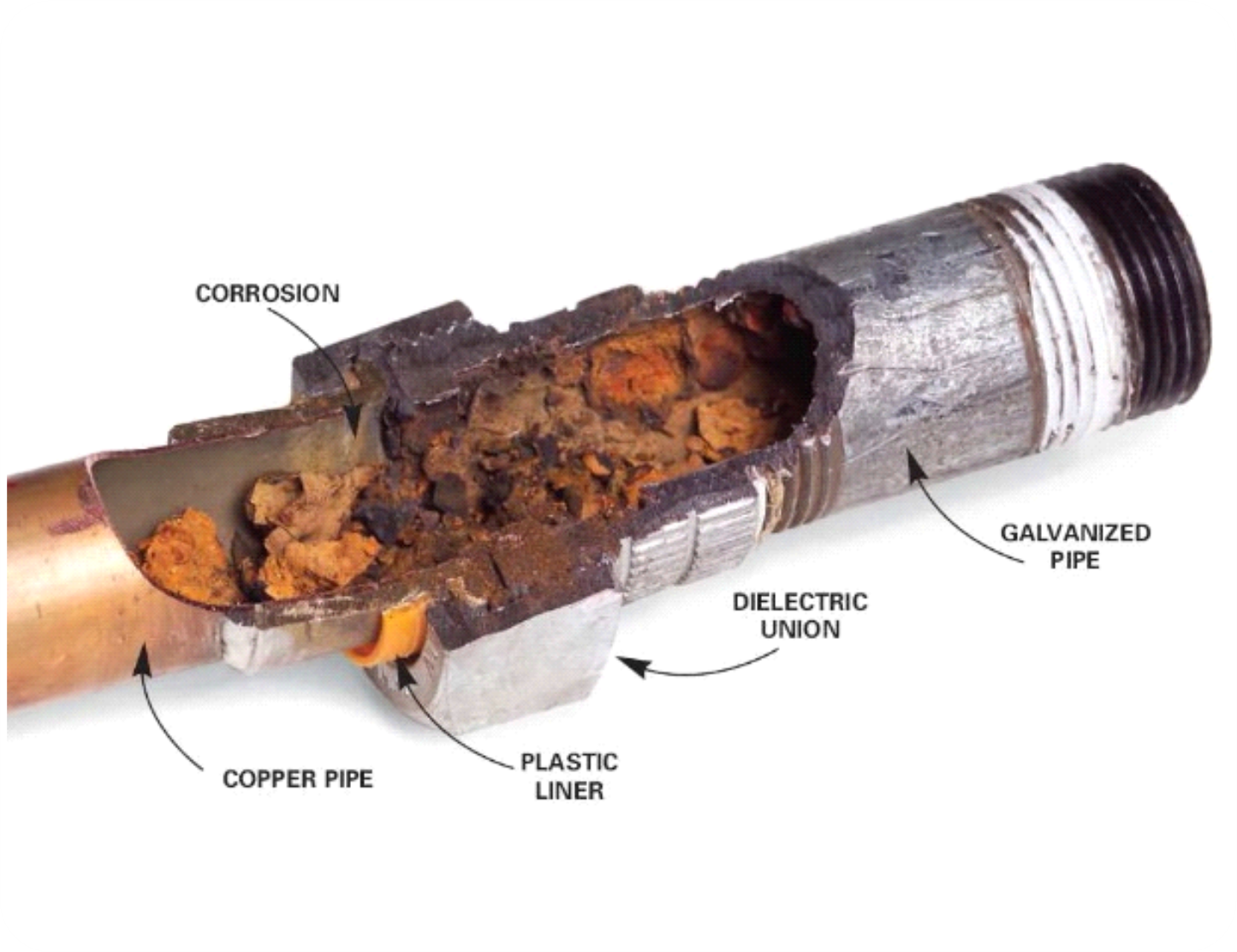
PARTICULAS DE ÓXIDO Y POLVO
Con el tiempo, los materiales que componen la tubería neumática se oxidan y además de reducir el diámetro y caudal de las mismas, desprenden partículas que más adelante generan un gran problema por el daño a componentes neumáticos y equipos; por lo general, cuando este problema se presenta ya es muy tarde para corregirlo con un mantenimiento simple o instalación de filtros de retención de partículas, para este entonces lo más recomendable es un reemplazo total de los materiales corroídos; también es posible encontrar partículas de polvo mezcladas en el aire por la falta de mantenimiento a equipos desecantes o por la mezcla de algunos productos químicos que algunos clientes producen.